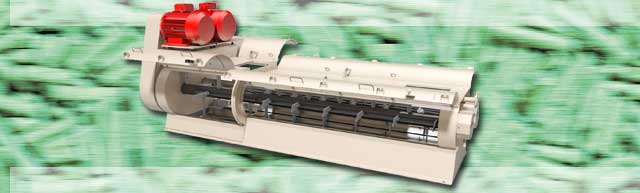
Two mixing shafts offer a great mixing effect
The SALMATEC molassing machines are designed for admixing large amounts of liquid
The opposing and rapidly rotating mixing shafts guarantee a great mixing effect and high throughput.
Immediately after the mixing process has been completed, the product can be coated in the same machine. This happens in what is known as the expansion stage. The mixed material is powdered with unmixed material. This prevents the subsequent conveyor units from sticking together.
Like all SALMATEC products, the molasses mixers from the SALMACON series also conform to the latest safety requirements and guidelines.
SALMACON 2000 molasses mixers
Model | Output in tonnes per hour | Drive in kW |
Salmacon 2015 | 25 | 2 x 7,5 |
Salmacon 2022 | 35 | 2 x 11 |
Salmacon 2030 | 50 | 2 x 15 |
Salmacon 2044 | 80 | 2 x 22 |
Salmacon 2060 | 100 | 2 x 30 |
Special features
SALMATEC offers a ZE version for each SALMACON for powdering the molasses with untreated material.
It goes without saying that steam can also be added.
All double shaft mixers from the SALMACON series are also suitable as conditioners for adding high amounts of steam.
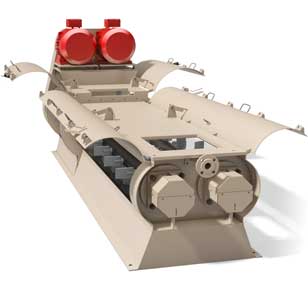
Advantages
Two opposing mixing shafts with overlapping paddles.
The mixer paddles can be adjusted to the shaft. The special arrangement of the mixer paddles on the shaft ensures that they clean themselves.
All product contact parts are manufactured from high-quality stainless steel.
Options (selection)
- Electric trough heating
- Heat protection insulation of the trough
- Multiple nozzle equipment for adding liquid
- Positioning the feeding points where required
- Wear-resistant lining
- Non-stick coated lining
- Special designs for processing extremely lightweight bulk material
- Product-adapted shaft speed
- Paintwork in your favourite colour