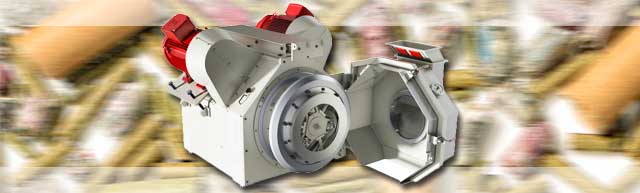
Cost-effective and safe to operate
SALMATEC pelleting presses from the Maxima series have a modular design and can be adapted perfectly to the most diverse requirements.
The different operating conditions that a pelleting press is subjected to during production of pellets make high demands on construction and production.
That’s why SALMATEC pelleting presses are made exclusively of high-quality materials and of course comply with the latest safety standards and guidelines.
The capacity per hour may amount to up to 50t depending on the type of machine and area of application.
Maxima-Duplex
Double pelleting in the smallest of spaces.
Maxima-Duplex is composed of two Maxima pelleting presses and ensures the highest pellet quality while simultaneously enhancing performance and ensuring greater flexibility.
And the special thing about it: Both Maxima pelleting presses also work individually or can be adapted to one another. The method of operation can be adjusted simply by using the pneumatically adjustable flap control device.
Comprehensive equipment
All Maxima pelleting presses have a vertically operating ring die in which two or three rollers depending on the product being processed ensure the highest pressure. The Maxima pelleting presses have a low-noise and one-step operated v-belt drive which provides energy-efficient and equal power transmission.
The heart of our pelleting press, the generously sized spherical roller bearing of the rotor, provides the machine with sufficient reserves even under relatively high stress.
The access door can be swung open across the entire pressing room and offers the best possible access to the pressing tools.
All Maxima pelleting presses have comprehensive standard and safety equipment. This includes the overload flap, permanent magnets, shear pins and overload clutches, temperature control, safety switches and much more.
MAXIMA pelleting presses
Model | Drive power | Die diameter | Working width | |
Maxima 360 mini | 1 x 15 – 30 | 360 | 40 | |
Maxima 360 eco Maxima 450 eco | 1 x 22 – 55 1 x 22 – 75 | 360 450 | 50, 75 75, 100, 115 | |
Maxima 450 mk Maxima 500 mk | 2 x 37 – 2 x 75 2 x 37 – 2 x 75 | 450 500 | 100, 115 100, 135 | |
Maxima 450 k Maxima 500 k Maxima 500 | 2 x 37 – 2 x 75 2 x 37 – 2 x 75 2 x 37 – 2 x 75 | 450 500 580 | 100, 115 100, 135 100, 150 | |
Maxima 620 k Maxima 700 k | 2 x 75 – 2 x 110 2 x 75 – 2 x 132 | 620 700 | 100, 150 100, 130, 175, 225 | |
Maxima 840 k | 2 x 90 – 2 x 200 | 840 | 125, 200, 240, 270 | |
Maxima 900 k | 2 x 110 – 2 x 250 | 900 | 300 | |
Maxima 1000 k | 2 x 110 – 2 x 250 | 1000 | 300 |
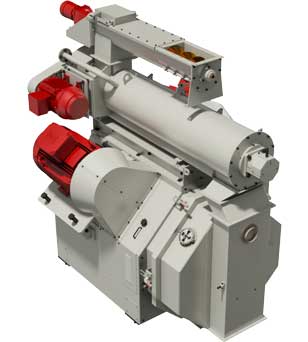
Areas of application
- Feedstuff
- Wood chips and dust
- Renewable raw materials
- Pelleting films/waste
- Textile materials/carpet remnants
- Waste in the steel industry
- Paper and rejected materials
- Filter dust
- Sludge
- Natural and artificial fertiliser
- Feedstuff
- and much more
Options (selection)
- Optionally double or triple roller system
- Automatic roller gap adjustment
- Noise protection insulation
- Electric door heating
- Heat protection insulation
- Roller temperature control
- Roller cooling
- Multi knife
- Automatic central lubrication unit forced feeder
- Die and roller hoist frame hydraulically actuated
- Triple axle vibration measurement system
- Special designs for processing extremely lightweight bulk material
- Maintenance drive
- Pneumatically adjustable pellet knife
- Paintwork in your favourite colour